Techniques : Bois et toile | Cousu-Collé | Strip-Planking | Sandwich composite
La construction en sandwich composite consiste à créer une coque formée d’un empilement de couches : peau en fibre / âme en mousse / peau en fibre.
La résistance de l’ensemble est liée à la résistance des peaux et leur écartement, donné par l’âme, plus les peaux sont écartées, plus la résistance en flexion augmente.
Lorsqu’on contraint le sandwich en flexion, les forces se répartissent sur les surfaces externes, en compression à l’intérieur, en étirement à l’extérieur :
Si les fibres sont disposées de sorte que l’étirement soit dans l’axe de la fibre, la résistance est optimale.
D’autres résistances sont à considérer pour un kayak : la résistance au poinçonnement (le caillou pointu qui appuie sur la paroi), et la résistance à la compression (écrasement du sandwich). Elles sont obtenues par la combinaison de la solidité des peaux et de la densité de la mousse : une peau mince sur une mousse qui s’enfonce facilement se percera facilement, et la compression pourra délaminer rapidement le sandwich (les couches se désolidarisent). Mais plus on augmente l’épaisseur des peaux, de l’âme ou la densité de l’âme, plus le poids grimpe (et le prix aussi).
En fait, les constructions collé-cousu et strip-planking sont aussi des sandwichs, l’âme étant le bois. Mais comme la coque en bois a déjà des caractéristiques mécaniques non négligeables, il faut moins de peaux en fibre pour obtenir un bateau suffisamment résistant. En 100% composite, la mousse haute densité (souvent 90kg/m3) utilisée comme âme n’a presque pas de résistance, elle ne peut se tenir en forme seule avant stratification.
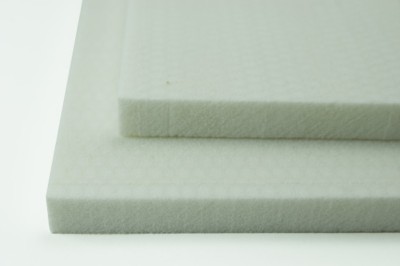
Mousse haute densité
En conséquence, pour faire une coque 100% composite, il faut créer un moule de la coque, sur lequel on pourra mouler la première peau, façonner la couche de mousse pour l’âme et mouler la 2ème peau.
C’est une des raisons pour lesquelles cette technique ne m’attire pas, quelque part il faut quasiment créer le moule en strip-planking pour pouvoir mouler la coque 100% composite. Autant faire directement le bateau en strip-planking!
C’est consommateur en temps et en budget, et que faire du moule une fois le kayak construit? Poubelle? A moins de le transmettre à un autre constructeur qui voudrait le même kayak, c’est perdu. En club c’est une technique courante, mais quand on veut se faire un kayak bien à soi et pas reproduire un modèle répandu, c’est plus compliqué.
Aux coûts déjà engendrés par la création du ou des moules (pont + coque), s’ajoute le coût supérieur en tissus et résine (il en faut plus) et le coût de la mousse haute densité, qui est très chère (20-30€ /m²).
Avantage pour la construction 100% composite : on peut faire un kayak léger et rigide, mais le coût et le temps de travail sont bien plus élevés.
Autre méthode de construction 100% composite :
J’ai imaginé une autre méthode pour la construction 100% composite mais pas encore testé, un jour peut-être…
L’idée c’est de construire comme avec la méthode du cousu-collé, mais en remplaçant les plaques de contre-plaqué (CTP) par des plaques en sandwich composite : fibres/mousse/fibres. A voir si des plaques de ce genre peuvent s’acheter, sinon il est possible de les réaliser sur une grande table bien plate.
Une fois les plaques achetées ou faites, on découpe dedans la forme des plaques requises pour le kayak qu’on assemble de la même façon que des plaques de CTP.
Et au final, pas besoin de stratifier l’ensemble de la coque, un galon de fibre de verre stratifié le long de chaque jonction de plaques, intérieur/extérieur, devrait suffire.
Logiquement un bon gain de poids par rapport au CTP, mais un coût tout de même supérieur puisqu’il faut de la mousse haute densité en quantité suffisante pour toute la coque.